A Hard Look at Hardwood

Hand-crafted beauty.
Hardwood flooring has evolved from the original thin strip planks to a huge
assortment of textures and colors. Here, a crew of workers hand-scrapes wood
flooring to give it a rustic look.
When I started my career back in the ‘80s, 98 percent of what I did was install, sand and finish 2 1/4” and 1 1/2” Red Oak flooring. My coworkers and I always looked forward to working with something out of the ordinary, which for us was a job that called for white oak or maple. The very idea of installing a factory-finished floor went against the principles of my craft. Safe to say, that has all changed. Today, we see more and more exotic species, an assortment of gloss levels, hand-scraped, hand-sculpted, distressed, reclaimed, renewable…you name it. Engineered hardwood is now the norm and factory-finished flooring is the standard. So what happened?
A closer look at recent changes in the hardwood category may hold clues for what’s in store for the future. While the standard 2 1/4” oak plank offered limited color and finish options, it did look great. In my opinion, the factory-applied wax was (and is) a great finish that offers many benefits (I’ll save that for another time). Consumers, however, feared the dreaded water spot. More often than not, they simply did not know how to properly maintain the wax finishes, so floors were either poorly maintained or over-maintained with too much wax applied. This in turn led to customer dissatisfaction and a demand for wood that is easy to maintain.
Over time technology improved and the advent of UV cured urethanes revolutionized the wood floor industry. Consumers could now get a durable finish with a 10-year warranty. The new generation of products also eliminated the time, dust, smell and inconvenience associated with having an unfinished floor installed. They also caught the eye of builders who soon realized that pre-finished floors fit in well with their fast track schedules. A hardwood floor could be installed and walked on the very same day. For those who worked with hardwood flooring for many years this was a huge breakthrough.
Along came the ‘90s and the introduction of aluminum oxide, a hardwood finish that provides superior wear resistance. Manufacturers could now increase the finish warranty to 15 or even 25 years. At the same time the three standard colors available increased to a color palette that is still growing. These advances made sense for the consumer and the homebuilder. Installation was much more simple and design options had never been more plentiful. Also, the repair-ability of pre-finished wood was (and still is) another big factor.
Not surprisingly, as hardwood’s popularity grew, so did the competition. As more and more manufacturers saw the profit potential, overseas competitors entered the U.S. market, many touting new styles and species of wood not seen before. Oak and Maple species were no longer the only game in town. Engineered sawn or sliced face veneer products were introduced offering the look of a solid product with the dimensional stability of an engineered product. Species no one could pronounce were beginning to appear. Hand-scraped floors let homeowners create a floor with a distinct rustic look. Most important, consumers could finally have flooring unlike their neighbor. These and other changes have been the driving force behind hardwood’s ever increasing popularity over the last 20 to 30 years.
So what now?
As someone who has been in this business for decades, I have to conclude that hardwood flooring may have reached a plateau in terms of how many different ways it can be used (after all, we are talking about wood, not plastic). Mother Nature provides us with a bounty of natural resources, but realistically there are limits on what can be produced. Also, while factory-finished flooring is hugely popular, there remains a considerable universe of existing floors that require on-site sanding and finishing. Of course, even factory-finished floors need on-site refinishing from time to time.
As flooring has advanced so too has the equipment used to install and maintain it. Many of the sanding tools used today, for example, include vacuum systems that eliminate virtually all of the wood dust from the job site. Changes related to VOCs in the stains and finish have also been a huge advantage because the “paint smell” associated with these products has been greatly reduced. (That’s also good news for the workers applying the products.)
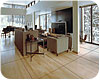
A modern touch. Although
hardwood flooring has been around for centuries, designers continue to come up
with new and imaginative ways to install it in a home. The light-colored maple
flooring seen here is accented with walnut borders to create a highly unique
and compelling floor.
The move toward all things Green will also continue to shape the hardwood flooring business. The way I see it, this movement affects the business in several ways. Most importantly it raises our awareness as an industry to be more responsible for our actions and the actions of others.
Recent amendments to the Lacey Act (which was signed into law more than 100 years ago) strengthen the focus on illegally harvested materials. Violators obtaining logs or materials illegally harvested face stiff fines and possible jail sentences. But the driving force will be consumers. They are asking more questions at the point of sale and want to know the source of the raw materials used to produce their flooring. The end result may limit the amount of exotic species on the market. It may even significantly reduce the number of suppliers who can legally sell these species. As such, prices may increase and that, in turn, may increase demand for readily available species such as the domestic Oak, Hickory, or Maple. Bottom line: as consumers become more environmentally aware, we need to get the message out about how we use natural resources. We need to educate consumers about the industry’s sustainable approach to harvesting raw material.
The good news though is simply this: when harvested and manufactured responsibly, wood flooring is about as Green as you can get. It comes from a renewable resource and can last for generations. But that is not the main reason hardwood flooring will continue to be a top choice for people who can have any type of flooring. They recognize this as something that adds warmth, character and beauty to almost any home (not to mention increasing its value).
Looking for a reprint of this article?
From high-res PDFs to custom plaques, order your copy today!