How a Good Subfloor Protects Your Flooring Investment
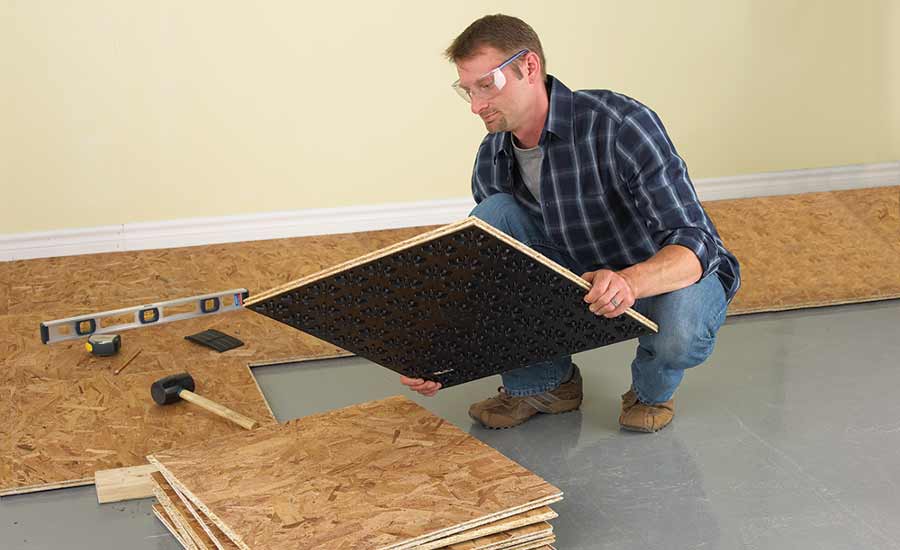
While homeowners can’t see what’s underneath their basement finished flooring, practically everything in a home built with a finished basement rests on a good subfloor product. It’s an essential structural material if you aim to build or renovate a dingy, damp and cold space and turn it into a warm and comfortable living activity room. In this case, what the homeowner does not see is what matters the most, and is truly a quintessential part of the room, particularly when they are investing in costly flooring materials to make the space a desirable place to be. Whether it’s carpet, engineered hardwood, laminate or tile, a basement should never be built without a solid subfloor product that is essential to a floor’s lasting value.
With today’s new home trends, the demands placed on a subfloor are growing: open floor plans, large format ceramic tiles and living areas with granite counters all bring more weight to bear on floors. Those design elements need to be supported by a new level of strength, density and moisture control technology and any contractor, designer or builder who ignores this is setting themselves up for a potential call-back from the homeowner. From loose or cracked tiles to swollen or cupped flooring due to moisture, these are problems that could lead to time-consuming re-dos and expensive warranty claims.
Here are a few reasons contractors, designers and home builders should consider installing an engineered subfloor material under a floor covering.
An Inviting Floor
A basement floor can be the place where the family hangs out to watch movies, play games and put together puzzles. Whether the floor acts as the sofa and needs to be cozy and warm or the basement is an extended family living space for elderly parents, a good subfloor product with a high R-Value creates a comfortable foundation for the room’s finished floors. Basement floors are naturally cold and the higher the R-Value of the subfloor, the better the insulation between the floor covering and the concrete, and the warmer the floor will feel under the feet.
Moisture Resistance
There is always moisture in a basement, from heavy rain or ground-water, or interior sources such as humidifiers, washing machines, and unvented dryers as well as bathrooms. Humid air coming from the outside can also enter the basement and cause condensation on cooler surfaces. According to Water Damage Defense, 98% of basements in the U.S. will suffer from some type of water damage during their lifetime. Today’s more complex basement builds require an excellent subfloor product material. A concrete basement slab is porous and prone to moisture absorption from water vapour migrating up through the slab. Look for subfloor panels that elevate the floor and create an airspace allowing moisture to evaporate naturally. This helps prevent the formation of mould or mildew.
Strength and Stability
As a structural element, subfloor holds up the flooring as well as everything in a home’s basement--heavy furniture, gym equipment, bar counters, along with the usual cats, dogs, and people. A high quality engineered subfloor is manufactured to withstand the demands of heavy traffic and furniture without sagging or bouncing. Compression strength is a function of the panel’s thickness and type. Some high-quality engineered wood subfloor is made with wood and advanced resins to make it perform to higher strength levels than traditional plywood as there is less deflection. Make sure to ask about panels that perform above the minimum required standard. After all, a basement floor is only as good as its foundation, so choosing a good subfloor is essential to the finished product.
For more information, visit dricore.com/
Looking for a reprint of this article?
From high-res PDFs to custom plaques, order your copy today!